Площадь центра — 2214 м.кв.
Пропускная способность — 36 050 сотрудников в год
Заказчик: «Газпромнефть-Снабжение»
Исполнители проекта:
Разработчик проекта —"Метра Диджитал Логистикс", интегратор, поставщик автоматизированных решений для складской логистики, производитель беспилотных роботизированных транспортных систем.
Партнеры проекта:
«ГК ГИКОМ» — один из крупнейших производителей современного стеллажного оборудования.
«EME» — российский разработчик ПО для автоматизации складской логистики.
«Ronavi Robotics» — российский разработчик и производитель логистических роботов.
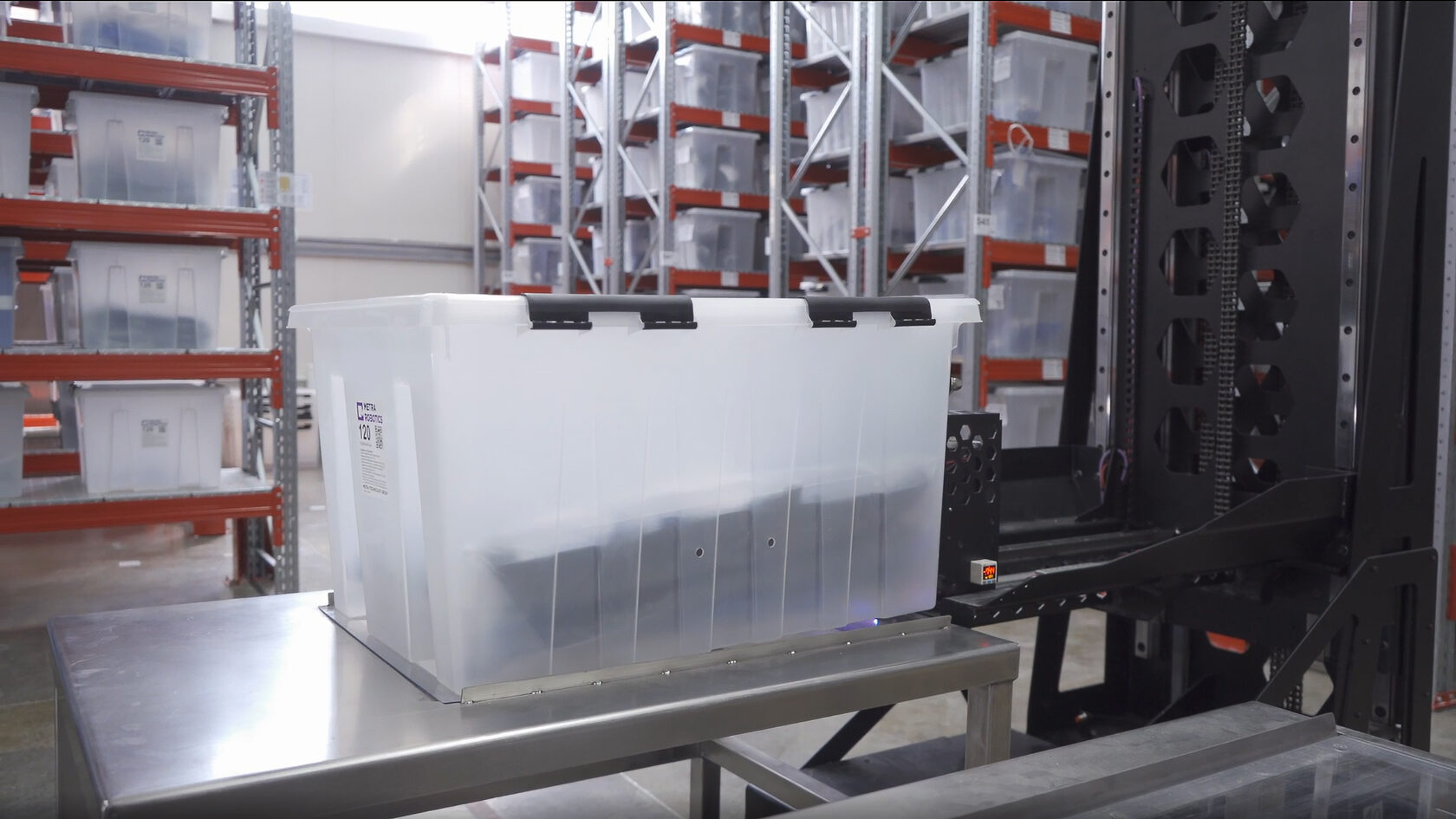
Предпосылки проекта:
- Географическая удаленность месторождений и отсутствие на них пунктов хранения и выдачи СО и СИЗ.
- Вахтовый метод работы нескольких тысяч сотрудников в Новом Уренгое предусматривает наличие большого штата обслуживающего персонала в экипировочном центре.
- Пересортица, путаница, очереди, в которых большое количество времени проводили высококвалифицированные специалисты.
- Дефицит площадей для хранения предполагал дополнительные затраты на аренду или строительство дополнительных терминалов.
- Ситуация требовала проработки эффективного решения.
Цель проекта:
Полная автоматизация процесса подбора спецодежды, выдачи, хранения, химчистки и ремонта.
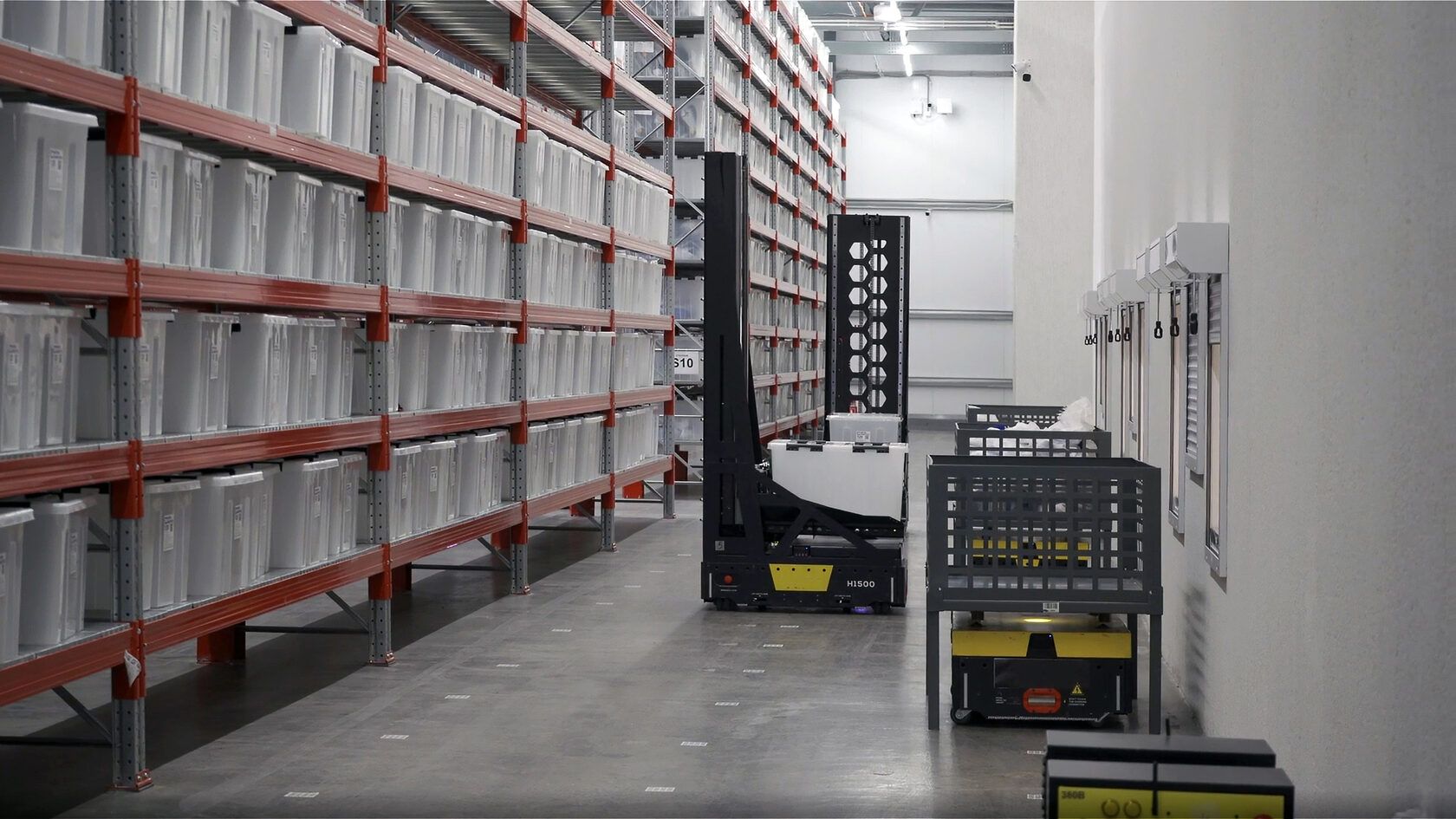
Ход проекта:
Компанией Metra Digital Logistics был проведен технологический аудит, по результатам которого была разработана карта технологического процесса.
Была разработана новая архитектура склада и полный комплекс решений — от отливки пластиковых коробов специальной формы, доработки и интеграции WMS, до сборки сервера, прокладки кабелей и создания беспилотного роботизированного погрузчика.
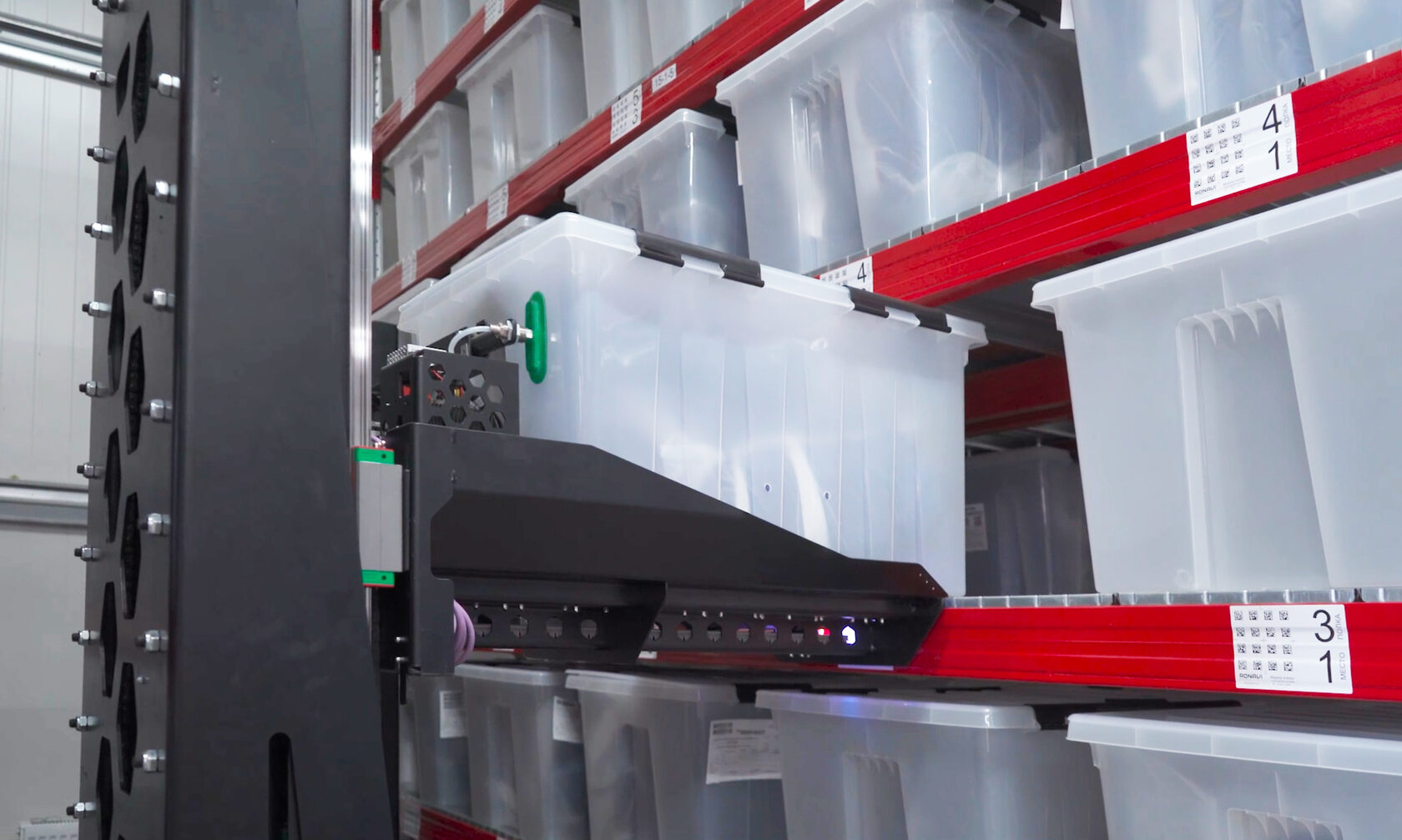
Архитектура «Цифрового склада» объединила в себе 17 элементов системы.
Сюда входят и системы электронной очереди, видеонаблюдения, мобильные роботизированные системы AGV, роботизированный подъемник «жираф».
Объединяющим центром проекта стала WMS-система управления складом, связавшая воедино управление складом с корпоративной системой заказчика, и системой управления роботизированным транспортом RMS.
Система «единого окна» проработана до мелочей, комфортна для сотрудников, но главное, что в 2 раза снизилось время обслуживания сотрудника «Газпрома».
Время от первого шага — получения талона работником, до доставки и выдачи одежды занимает теперь всего 60 минут.
В рамках проекта установлен автоматизированный комплекс — сканер по подбору размера. Всего за несколько секунд комплекс безошибочно подбирает подходящий размер одежды, и передает информацию в компьютерную сеть. Уже через пару минут робот находит требуемый комплект одежды, и подвозит контейнер к окну выдачи.
Внедрение RFID-технологий существенно повысило эффективность складской учетной системы, позволила сократить время поиска, и избежать ошибок при комплектации заказов.
Для логистических операций использованы интеллектуальные роботизированные транспортные системы грузоподъемностью 50 кг., также разработан роботизированный погрузчик «Жираф», поднимающий контейнер с одеждой на высоту до 6,5 м.
Все ключевые процессы экипировки для приезжающих на вахту и отъезжающих сотрудни полностью автоматизированы.
Доставка до систем хранения, подбор размера спецодежды, доставка одежды с хранения, отправка на химчистку теперь занимают минимум времени.
Высвободившееся время, которое теряли в очередях высококвалифицированные сотрудники теперь можно использовать с большей эффективностью.
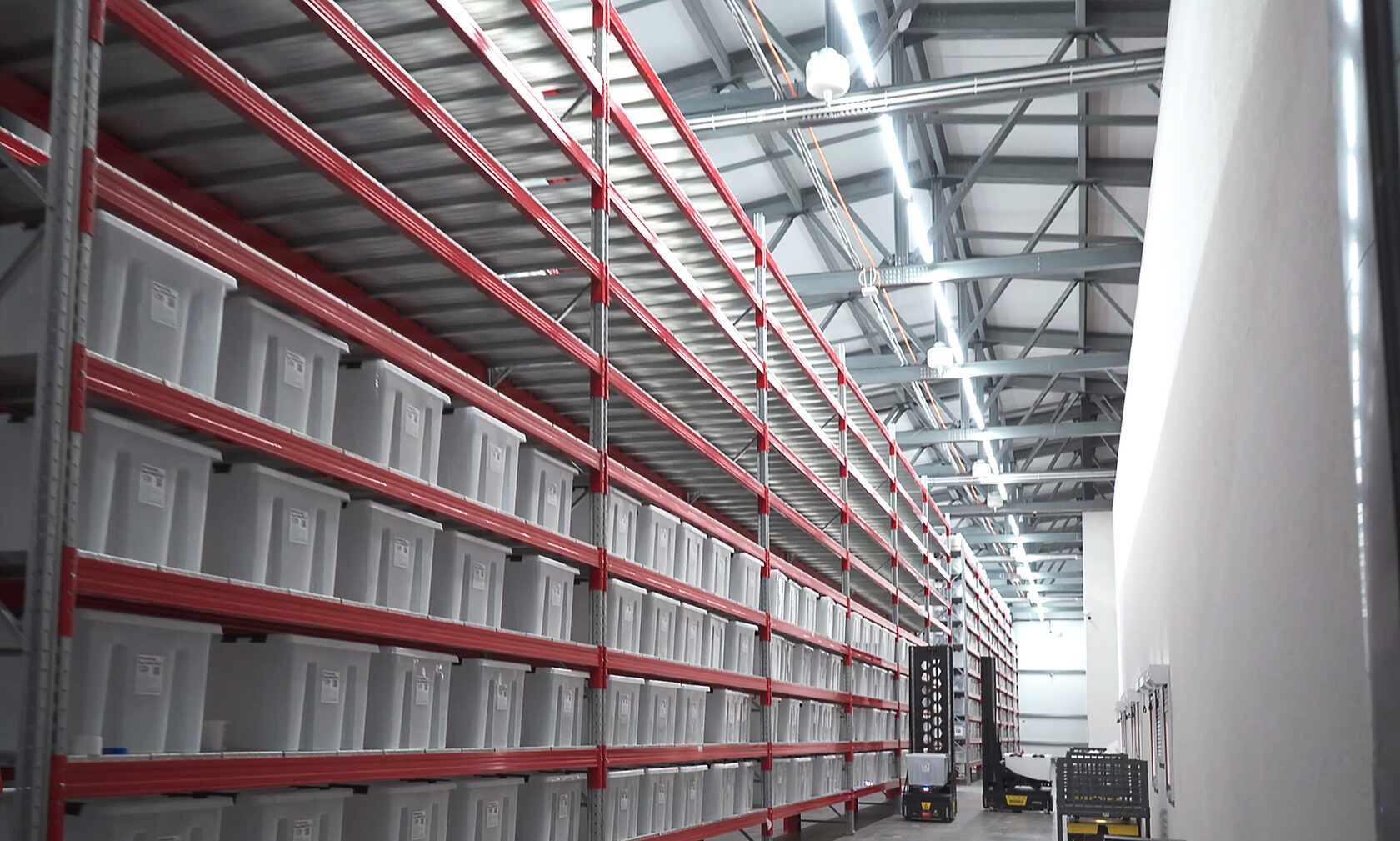
Итоги проекта:
- В 2 раза сокращено среднее время обслуживания 1-го о, трудника со 120 мин. до 60 мин;
- Увеличена пропускная способность центра увеличилась в 2.5 раза.
- Реализовано оказание полного комплекса услуг в режиме «одного окна»;
- Налажен точный автоматизированный учет ТМЦ;
- Обеспечены удобство и комфорт для сотрудников, порядок в центре и отсутствие пересортицы;
- Сокращены планируемые издержки. Отпала необходимость в аренде или строительстве дополнительных терминалов;
- Автоматизированы все процессы. Исключено влияние человеческого фактора.
Видео: